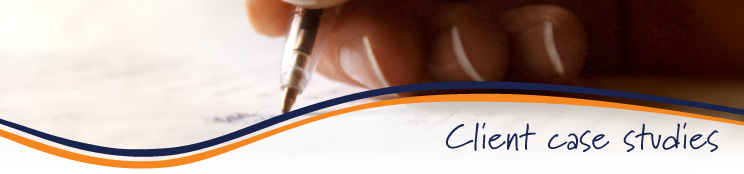
A national supermarket chain was in the throes of delivering a major efficiency initiative that covered practically all aspects of their operations from logistics through to retail environments. The change would touch all systems, staff and structures and would require new skills and a different culture. Operational staff would be particularly affected by this proposed change.
However, this hadn’t become clear until the design of the change programme structure. Mapping the vision to the blueprint threw up an amazing volume and variety of operational change within the stores. It was suspected that this would prove overwhelming. Further modelling showed detailed mapping of hot-spots (areas that would be swamped by change). The hot-spots tended to occur where several initiatives were delivering numerous changes into an area simultaneously, some of which would be national changes but others local to the specific stores or regions. The picture was ugly and complex.
Prioritisation was the first solution: identifying what really needed to happen in which sequence. This was followed by a series of simple procedures and protocols that protected the vulnerable workers in hot¬-spots from change fatigue. The important part was to understand the implications of this protection across all the initiatives on their rate of progress and the related organisational change.
Almost counter-intuitively, the effect of regulating change in the hot-spots was a rapid acceleration in the overall rate of change across the organisation. The primary reason for this was that change fatigue wasn’t encountered. Additionally, the more regulated the change that was introduced, the greater the rate of adoption became.